Scaffold brackets serve as indispensable components in the realm of construction and industrial maintenance, acting as the backbone of scaffold systems that guarantee stability and safety at elevated heights. Recognized for their robust nature, these brackets play a pivotal role in supporting platforms where workers perform tasks such as structural repairs, painting, and installations.
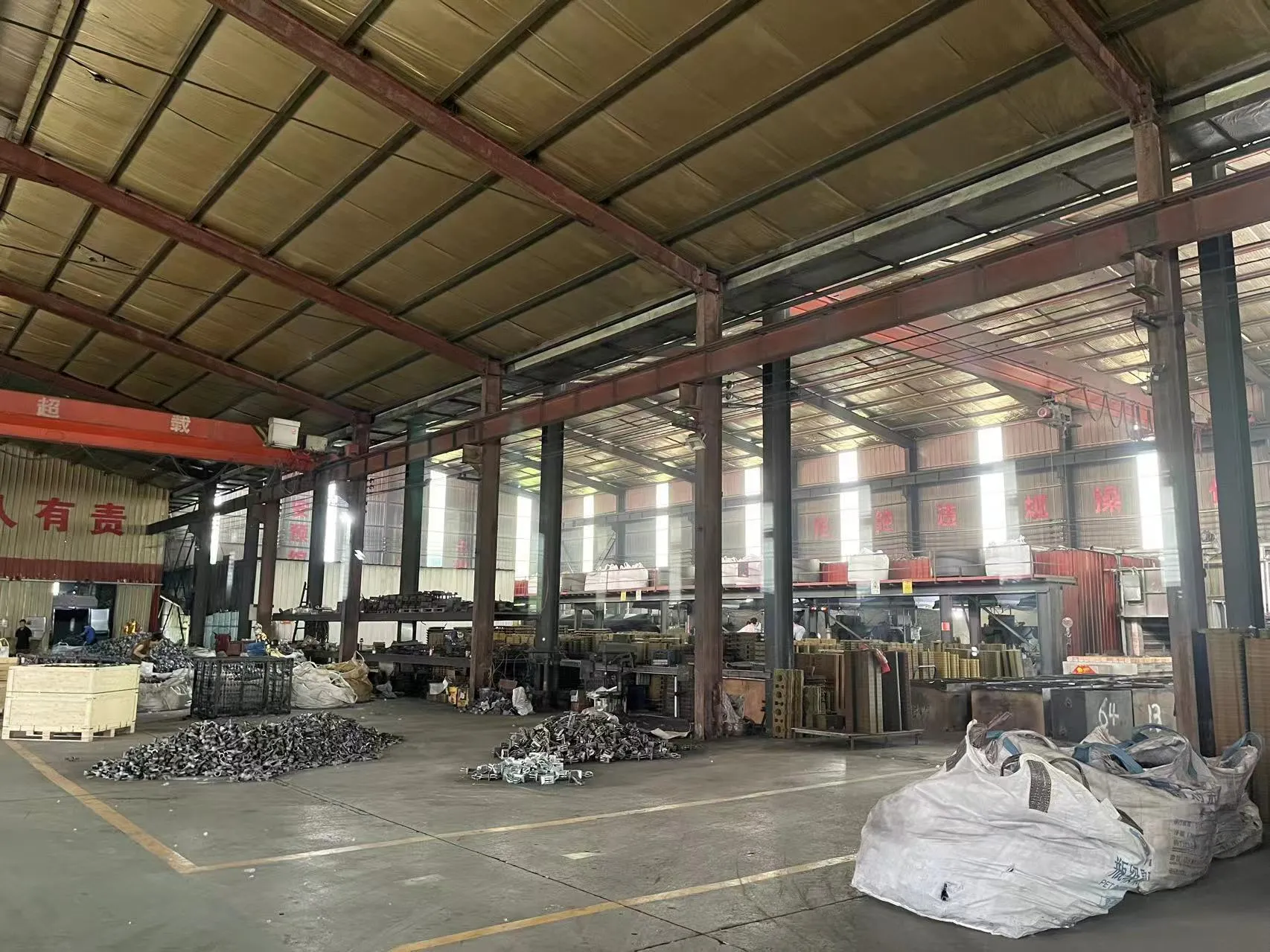
Having extensive experience with scaffold systems, I must emphasize the importance of selecting high-quality scaffold brackets for any construction project. The inherent strength of these brackets lies in their build, commonly made from high-grade steel or aluminum. The choice between steel and aluminum often boils down to the specific requirements of a project. Steel brackets are renowned for their durability and capability to bear substantial weight, making them ideal for heavier construction tasks, while aluminum brackets offer a lightweight alternative perfect for shorter-duration use without compromising on strength.
From a professional perspective, the expertise required to evaluate scaffold brackets extends beyond mere material selection. One must consider the bracket design, which should fit seamlessly into the framework, ensuring that they can endure dynamic loads and environmental stress. It is essential to opt for brackets that comply with international safety standards such as those enumerated by the Occupational Safety and Health Administration (OSHA) and the European Committee for Standardization (CEN).
Compliance not only assures the structural integrity of the scaffolding system but also enhances the confidence of the workforce working at heights.
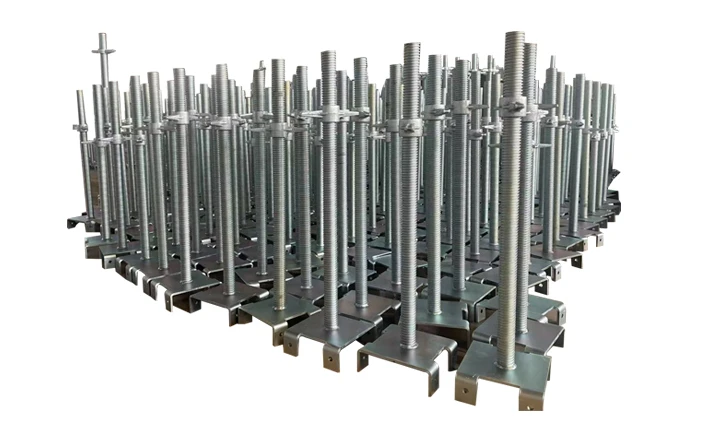
Authoritativeness in the scaffolding industry is established when leading manufacturers and suppliers routinely subject their products to rigorous testing protocols, thus certifying their reliability. Advanced testing methods are often employed to simulate real-world conditions – for instance, stress tests that account for extreme weather variances and load distribution studies. Such validation by an authoritative third party is crucial for stakeholders when deciding on scaffolding materials, as it directly correlates with the safety and efficiency of construction operations.
scaffold brackets
Trustworthiness in scaffold brackets hinges on transparency and a proven track record of performance. Testimonials from industry professionals who have utilized specific products play a significant role in shaping purchasing decisions. Feedback from construction managers and safety supervisors who’ve observed the long-term performance and ease of installation of particular scaffold brackets adds a layer of credibility that technical specifications alone cannot provide. Trust in a product often translates into productivity gains and reduced on-site accidents, ultimately reflecting in the project's bottom line.
Furthermore, embracing innovations such as modular scaffold brackets can revolutionize conventional scaffolding practices. These newer designs allow easy assembly and disassembly, saving time and labor costs and providing flexibility in altering scaffold heights and configurations as project demands evolve. Such adaptability is a testament to the advancements in scaffold engineering, underscoring the importance of investing in cutting-edge solutions that drive operational efficiency.
In summation, scaffold brackets, though perceived as minor components, hold significant power in determining the safety and success of a construction project. Their selection should be a well-considered decision involving material quality, compliance with safety standards, an assurance of trustworthy performance, and the potential for innovative application. Equipped with this knowledge, construction stakeholders can confidently choose scaffold brackets that align with their project's needs, ensuring a secure and productive work environment.