Navigating the intricacies of aluminium formwork cost involves understanding a variety of factors that influence pricing, as well as recognizing the inherent benefits and challenges associated with its use in construction projects. Aluminium formwork systems are increasingly becoming a popular choice in the construction sector due to their efficiency and durability. By examining the cost components and leveraging expert insights, stakeholders can make informed decisions that optimize both quality and expenditure.
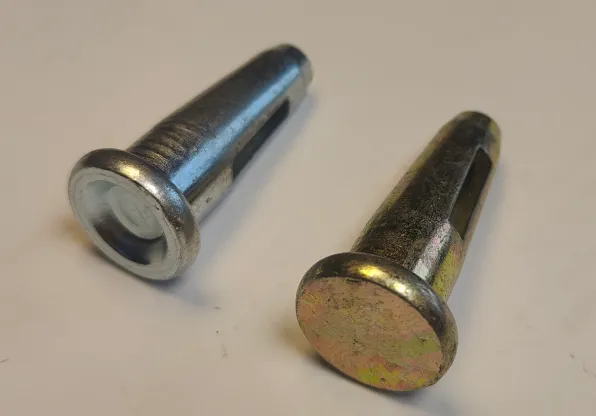
The cost of aluminium formwork is primarily influenced by the manufacturing complexity and the material quality. Aluminium, as a raw material, is lightweight yet strong, providing an ideal balance between ease of handling and structural integrity. However, its cost can fluctuate based on global market conditions, such as supply chain changes and extraction costs. Formwork systems also require precise engineering to meet specific project requirements, with design intricacy playing a significant role in the overall pricing.
Installation plays a pivotal role in the total cost of aluminium formwork. Its assembly often demands skilled labor, as the precision in setup directly impacts installation speed and project safety. The labour market, therefore, significantly affects associated costs, with experienced workers commanding higher wages. However, the investment in skilled labor often results in shorter construction timelines and less need for modifications.
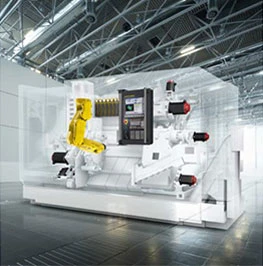
While upfront costs may seem significant,
aluminium formwork offers notable long-term savings. Its durability means it can be reused multiple times. This not only spreads its initial cost across several projects, effectively reducing average cost per use, but also aligns well with sustainability goals by minimizing waste. Moreover, its resistance to elements reduces maintenance costs, making it a cost-effective choice over time.
Quality control is another critical factor impacting the cost of aluminium formwork. Reputable manufacturers adhere to stringent quality standards, ensuring their products meet both local and international guidelines. Compliance often requires rigorous testing and certification, which can increase production costs but substantively enhance reliability and safety. Aligning with trusted manufacturers guarantees that the formwork will perform under expected conditions without unexpected failures or reparations.
aluminium formwork cost
When evaluating suppliers, consider the extent of their expertise and industry standing. Manufacturer reputation is often an indicator of product reliability and service quality. Trusted brands are typically backed by extensive research and development, offering innovative solutions that contribute to cost efficiency. Additionally, established manufacturers may offer comprehensive support services, such as onsite setup assistance or training, which can be invaluable for maximizing the formwork's utility.
Economic factors, including national tariffs and import duties, should also be considered when calculating total formwork costs. Local production can sometimes mitigate these charges, but understanding the geopolitical landscape is critical for accurate cost estimation. Engaging with local distributors might provide economic advantages and expedite delivery, further reducing associated logistics costs.
In terms of real-world application, several projects underscore the cost-effectiveness of aluminium formwork. Notably, high-rise residential developments have reported significant savings in material and labor, with project timelines reduced by as much as 30%. Such efficiency is attributed to the formwork system's capability to streamline the construction process, facilitating quicker and sequential operations.
In conclusion, while the initial investment in aluminium formwork might appear substantial, a comprehensive review of its lifecycle benefits reveals substantial cost-effectiveness. Thorough consideration of material quality, supplier reputation, labor market dynamics, and external economic factors is crucial to optimize investment. Strategic decision-making grounded in expertise and authority fosters trust and promotes long-term project success. Insightful analysis and informed selection promise not only financial savings but also project excellence and sustainability.