Screw jack systems have become instrumental in various industries, providing efficient solutions for lifting and positioning applications. Their design and operational efficiency span engineering marvels that cater to the growing demands of automation and precision control. Anyone who has ventured into the realm of mechanical lifting solutions would vouch for the myriad benefits these systems bring to industrial applications.
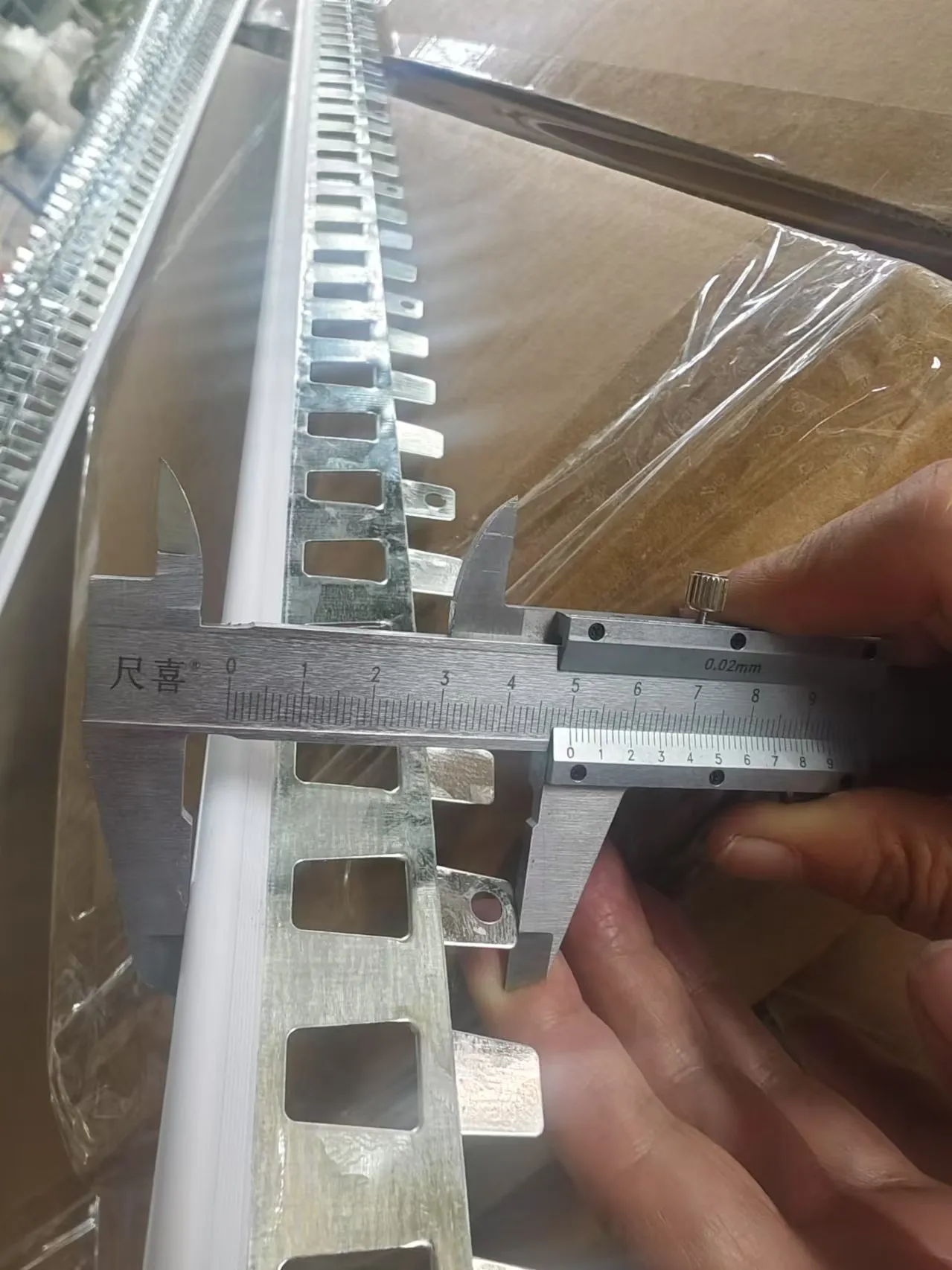
At their core, screw jack systems operate based on a simple yet robust principle. The system comprises a motor, gear mechanism, and a lifting screw, collectively working to convert rotational motion into linear lifting force. This transformative capability makes them ideal for applications requiring precise movement and positioning, ensuring seamless integration into diverse operational environments.
One of the key advantages of screw jack systems is their unparalleled versatility. From automotive manufacturing plants to aerospace assembly lines, these systems offer immense flexibility. Their ability to handle both vertical and horizontal loads grants engineers the freedom to design innovative solutions without being constrained by limitations inherent in other lifting mechanisms. This versatility ensures that industries can adapt screw jack systems to suit specific operational parameters, making them indispensable in today’s fast-paced, technology-driven world.
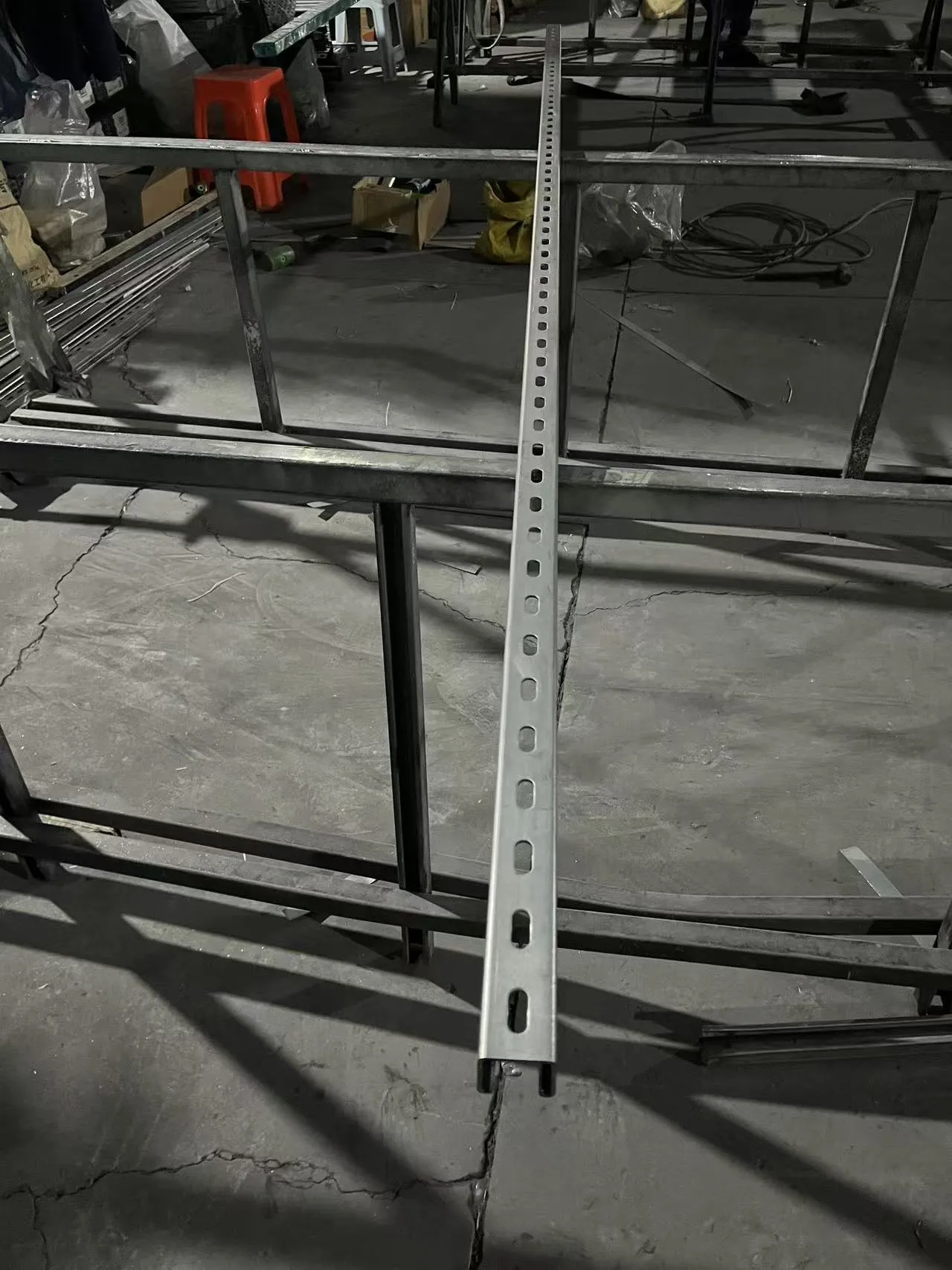
Equally important is the precision control that screw jack systems offer. Whether it is a requirement to lift heavy machinery for maintenance or to adjust the height of an assembly line conveyor, precision is paramount.
Screw jack systems provide a level of control that allows for micro-adjustments with remarkable accuracy. This precision is not only crucial for ensuring safety and reliability but also enhances overall operational efficiency by reducing downtime and maintenance costs.
The expertise involved in designing screw jack systems cannot be overstated. Engineering these systems requires a deep understanding of mechanical principles and materials science. The traction drive technology employed in some advanced systems further augments their load-handling capabilities while minimizing friction and wear. The materials used in manufacturing screw jacks are chosen meticulously to withstand extreme pressures and environmental conditions, affirming their durability and long operational life span.
Technical expertise must also extend into the realm of software interoperability. Modern screw jack systems often integrate with advanced control and monitoring systems to provide real-time data analysis and remote operation capabilities. This software integration enhances their utility in complex automation environments, enabling them to seamlessly communicate with other machinery and equipment for coordinated operations.
screw jack systems
Consider the authoritative implementation of screw jack systems within the renewable energy sector. As wind turbines become larger and more sophisticated, the assembly and maintenance of these structures require precision and reliability that screw jack systems readily provide. Their ability to work under extreme conditions, coupled with robust design, ensures that they perform consistently, a testament to their reliability and the trust industries place in them.
Moreover, the trustworthiness of screw jack systems is reinforced by rigorous testing standards they undergo before deployment. These tests simulate various operational stresses and environmental conditions, ensuring that each system exceeds industry standards for safety and performance. Manufacturers provide detailed certification of compliance, offering customers peace of mind and reinforcing the reliability of the systems.
Users of screw jack systems frequently highlight their ease of maintenance. With fewer moving parts compared to hydraulic systems, potential points of failure are minimized, contributing to lower maintenance costs and extended service intervals. This not only translates into reduced operational expenditure but also aligns with sustainable practices by decreasing the demand for replacement parts and material waste.
To remain competitively viable, innovation in screw jack systems continues at a rapid pace. Manufacturers are now focusing on integrating IoT capabilities and predictive maintenance algorithms to further bolster their utility. Such innovations aim to enhance user experience by providing alerts and diagnostics that preempt failures, thereby ensuring uninterrupted operations.
In conclusion, the intrinsic value of screw jack systems in the contemporary industrial landscape is undeniable. Their experience-tailored designs, coupled with expert engineering and authoritative certifications, forge a trusted solution in myriad applications. As industries continue to evolve, these systems will undoubtedly adapt, further cementing their position as essential components in precision lifting and positioning tasks.