Construction shuttering plywood has become an essential material in the building industry, celebrated for its robustness and versatility. With the growing demand for eco-friendly and durable construction materials, understanding the intricacies of shuttering plywood pricing is crucial for builders and contractors.
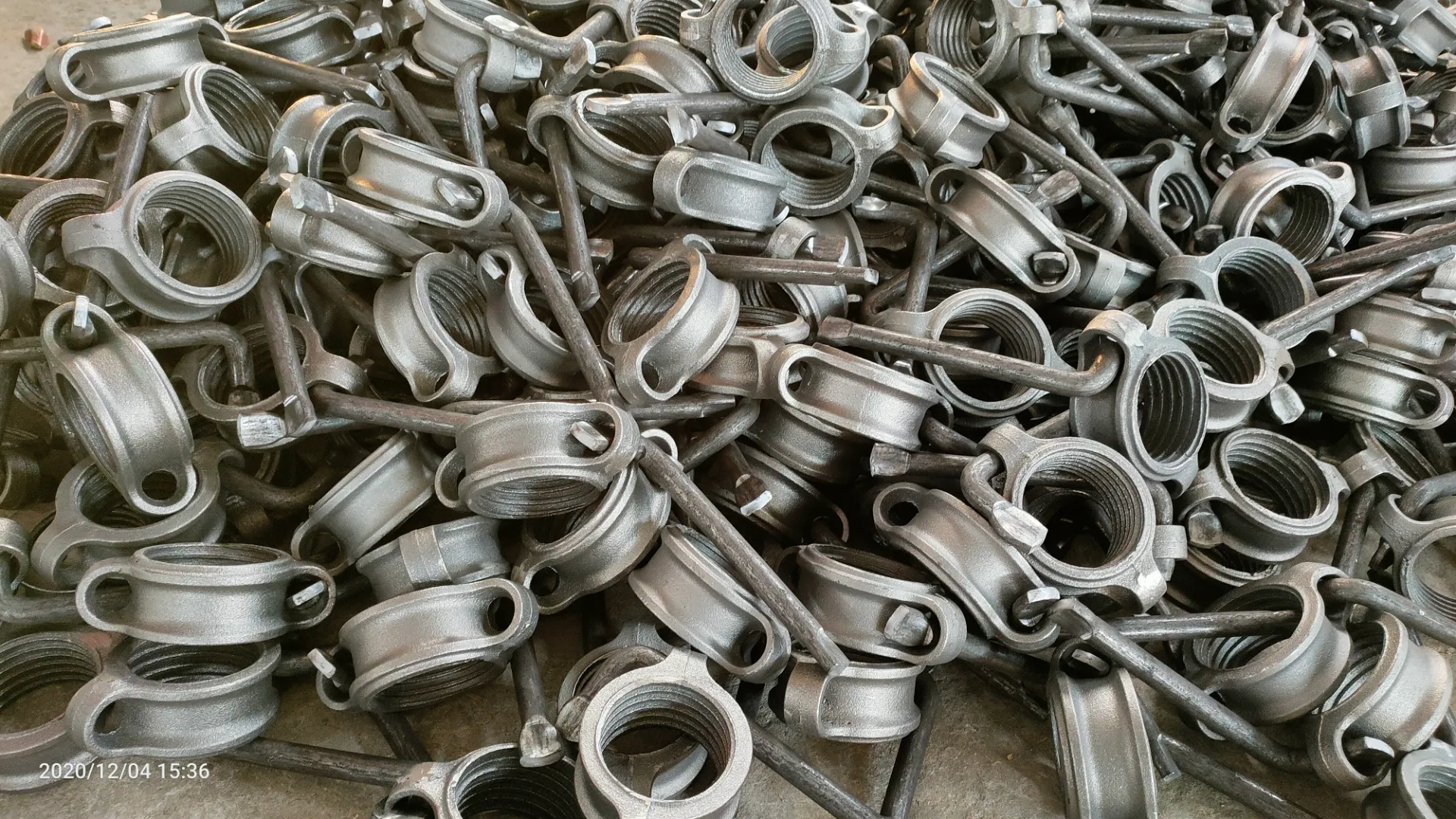
Navigating the market to find the best construction shuttering plywood involves several factors beyond just cost. High-quality plywood not only influences the structural integrity of formwork but also impacts the project timeline and costs associated with maintenance and material replacement. From an expert perspective, it's essential to break down the factors affecting plywood pricing to make informed decisions.
The primary determinant of construction shuttering plywood price is the grade of the plywood. Plywood comes in various grades, each corresponding to specific quality measures and applications. A-grade shuttering plywood offers superior surface finish and strength, making it ideal for projects requiring smooth formwork and longevity. As the grades descend to B or C, the quality and price decrease, suitable for less demanding applications or where cost reduction is a priority.
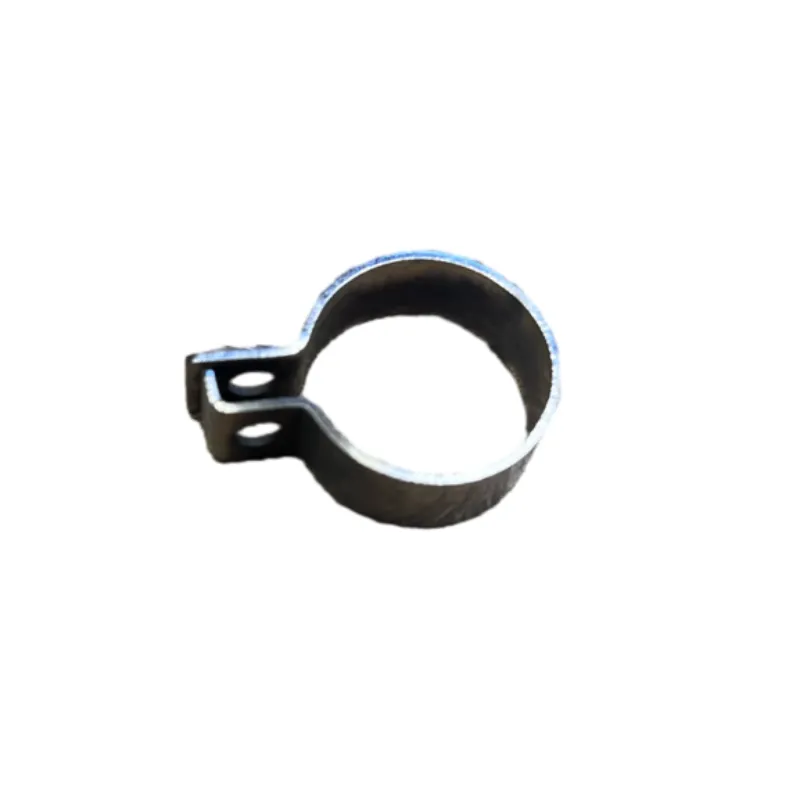
Thickness is another significant factor influencing the price. Thicker plywood sheets are more expensive due to the increased amount of raw material used, but they offer enhanced durability and load-bearing capacity, critical for large-scale construction projects. Builders often face a trade-off between the upfront cost of thicker plywood and long-term savings derived from its durability.
Another vital aspect is the type of wood used in the production of plywood. Hardwoods such as birch or oak tend to yield more expensive plywood compared to softer woods like pine. Hardwood-based shuttering plywoods are prized for their strength and resistance to damage from environmental stressors, making them a preferred choice for projects exposed to harsh conditions.
construction shuttering plywood price
The manufacturing process, particularly the type of adhesive used, plays a crucial role in the overall cost. Phenolic resins are commonly used in high-quality shuttering plywood due to their superior water resistance and strength. These resins withstand exposure to moisture and fluctuations in temperature, critical for construction sites. However, they also increase the production cost, thus, the end price of the plywood.
Geographical location can also impact plywood pricing significantly. Regions closer to manufacturing plants or rich in wood resources generally have lower production and shipping costs, resulting in more competitive prices. Conversely, remote locations with limited access to suppliers may face higher costs due to transportation expenses.
The choice of supplier and the volume of purchase also influence pricing. Established suppliers with a history of reliability and quality assurance often charge a premium for their products. Yet, they offer guarantees that can save costs related to quality issues and delivery delays. Bulk purchasing typically results in discounts, making it more cost-effective for large projects to negotiate purchase agreements that benefit from economies of scale.
When considering construction shuttering plywood, sustainability is an increasingly important factor that affects price. Eco-friendly or FSC-certified plywood may come at a higher price, reflecting the sustainable practices in its production. Though initially more expensive, sustainable plywood can enhance a company's reputation and appeal to environmentally conscious clients.
In conclusion, the cost of construction shuttering plywood is influenced by multiple facets including grade, thickness, type of wood and adhesive, geographical factors, supplier reliability, and sustainability. Builders looking to optimize their investment in shuttering plywood should conduct a comprehensive analysis of these factors. Prioritizing quality and durability over mere cost can result in long-term savings and improved project outcomes. For those committed to sustainable building practices, the slightly higher investment can be justified by the reduced environmental impact and enhanced project appeal. Understanding this nuanced landscape allows industry professionals to make economically and environmentally sound decisions, leveraging their expertise to achieve project success.