Drop forged scaffold fittings are vital components in the construction industry, known for their unparalleled durability and strength. With years of expertise in the field, I’ve had the opportunity to see firsthand the remarkable impact these fittings have on project safety and efficiency. Companies that prioritize quality often rely on drop forged scaffold fittings, given their robust nature compared to other types of fittings.

Crafted through a meticulous process where metal is heated and shaped under high pressure, drop forging aligns the grain structure of the metal, enhancing its overall strength and fatigue resistance. This makes the fittings exceptionally resilient against heavy loads and adverse weather conditions—essential features for any scaffolding system exposed to the elements.
Choosing the right scaffold fittings not only assures the longevity of the scaffolding but also significantly boosts worker safety. Poor-quality fittings can result in structural failures that pose serious risks. However,
with drop forged options, the risk is significantly minimized. These fittings are less prone to wear and tear and offer a superior grip that secures scaffold beams firmly, even in challenging environments.
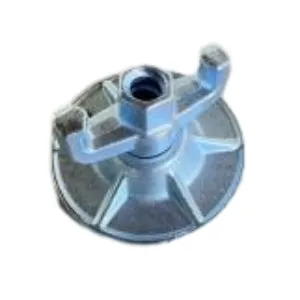
From a professional standpoint, the expertise required to select appropriate scaffold fittings cannot be overstated. It involves understanding load capacities, environmental conditions, and the specific requirements of a construction site. Over the years, I have noticed that projects leveraging high-quality drop forged scaffold fittings consistently meet safety regulations with ease, often surpassing industry standards. This speaks volumes about the authoritative standing of these products in the market.
drop forged scaffold fittings
The trustworthiness of a construction setup heavily relies on using components that conform to global safety standards. In the case of drop forged fittings, they are regularly subjected to stringent quality checks that assure their compliance with regulations such as the EN74, BS1139, and OSHA standards. Such compliance is crucial in maintaining the integrity of construction operations and ensuring peace of mind for contractors and workers alike.
I have also witnessed that using drop forged scaffold fittings can lead to cost efficiency in the long term. Their inherent strength reduces the need for frequent replacements, offering a more sustainable option that aligns with eco-friendly construction practices. This not only supports the operational budget but also adheres to modern environmental considerations, a necessary aspect of current and future construction projects.
In summary, drop forged scaffold fittings are a testament to expert craftsmanship in the construction industry, holding a well-deserved authoritative and trustworthy reputation. Their reliability is unmatched, and their ability to enhance safety while ensuring cost-effectiveness makes them indispensable. For any contractor looking to uphold the highest standards of construction practice, these fittings are undeniably the choice for ensuring a successful, safe, and sustainable project.